As more and more assets get connected, discrete manufacturers can now closely monitor and track their assets in the field and deliver in-depth performance reporting. Asset availability measured as uptime is one of the primary KPIs that both customers and vendors are interested in. In today’s post, we will show how easy it is to realize this with Waylay Digital Twin and Salesforce Field Service.
In manufacturing, overall equipment efficiency (OEE) is used to measure production performance in relation to planned production time. It's standardized as part of the ISA-95 standard. Outside of the production industry, there is no standard in place and OEE is hardly used, but companies can still benefit from monitoring uptime SLAs.
OEE scores are calculated by multiplying three key metrics delivered as percentages: asset availability, asset performance, and the quality of the produced goods. When OEE scores drop, asset downtime is analyzed (in retrospect) by looking at reason codes sent by the equipment.
These low-level reason codes have been defined by either the equipment builder or an OT engineer, and they provide little clue as to why the availability and reliability of the machines have deteriorated. Codes like "Operator Error", "Machine Malfunction", "Unexpected Blocked", or "Other" don’t provide much insight into what the problem is, let alone give recommendations on how to fix it or explain the business context.
This is where Waylay Digital Twin comes in. Waylay Digital Twin for Salesforce enables smart industrial asset reliability management that does all three things: finds the cause of the problem, shows the business context, and gives mitigation recommendations. At a technical level, it does this through better tracing and modeling of events that impact asset performance.
Better root cause analysis for unplanned downtime with Waylay Digital Twin
The solution we will look at is based on the concept of downtime records in the case of unplanned asset downtime.
Unplanned downtime is a serious problem. Depending on the type of contract the customer has, unplanned downtime may:
- Violate contractual uptime guarantees
- Cause refunds or asset replacements
- Negatively impact the customer’s business performance
- Drive costly field visits
- Erode customer trust
Causes of unplanned downtime can be subtle and are directly related to the hardware and the increasingly complex software inside the connected asset:
- Software faults, input faults
- Frequent restarts
- Online but machine doesn’t produce a stable output or no useful output
- Online but the asset runs in a suboptimal mode (safety mode, recovery mode, …)
- No data was reported for a while due to connectivity issues
- Error codes are reported
- The asset has been hacked
Some of the causes for unplanned downtime are not related to the asset:
- Power outage
- Vandalism
- Adverse weather conditions (too hot, too cold, flooding)
- Dead battery
- Someone turned off the asset by accident
It should be clear to the reader that these unplanned downtime root causes depend on the type of asset and the business context. However, knowing the root cause of the unplanned downtime events leads to much more effective repair strategies to avoid them in the future.
With the Waylay Digital Twin solution, the business user can create rules to track down the root cause of the unplanned downtime events. In the next section, we’ll show a concrete example of how this can be done.
Leveraging downtime records with Waylay Digital Twin
In the screenshot below (Fig.1), you see an example of an Asset within the Salesforce Service Console called “SmartFactoryInc”. The top bar shows the following KPIs of a sub-asset called “Asset ‘EngineY”: actual reliability, availability, average uptime per day, cumulative downtime and cumulative unplanned downtime.
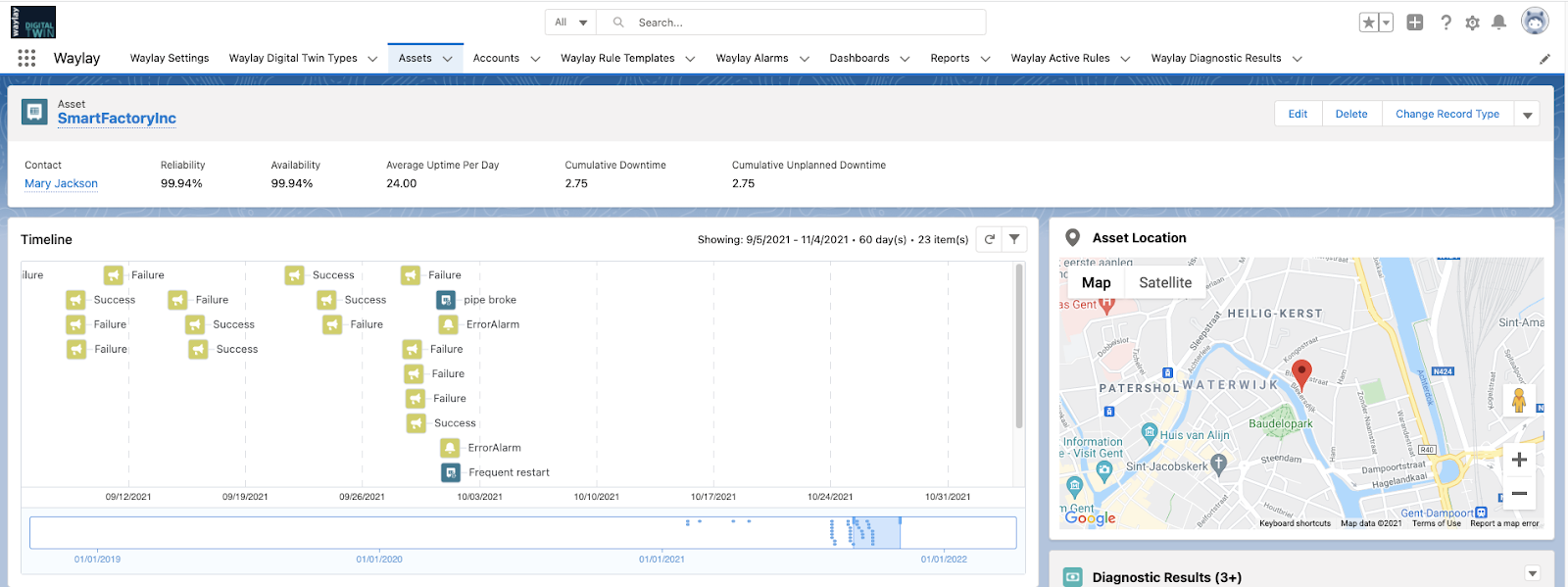
In the timeline graph, the service manager can see a history of Waylay Alarms (in light green) that were triggered by proactive monitoring rules. Some of these rules have led to multiple unplanned downtime records (in dark green).
An example of such a rule is shown in the next screenshot (Fig.2) where you can see the UI of the Waylay Digital Twin no-code rule designer. This is a proactive conditional monitoring rule created by a Salesforce business user to generate a Waylay Alarm Record whenever the asset's operating mode is active but restarts often.

This is an example of a rule that detects when an asset isn’t performing any useful function even though it is shown as being operational. Potential root causes of frequent restarts are software or hardware bugs that prevent the asset from remaining online. Therefore a maintenance visit should be scheduled ASAP to either perform a firmware update or replace the asset. Further on, it may be that the visual inspection performed during the maintenance check doesn’t reveal any problem with the asset. But if frequent restarts continue, the asset is considered down from a contractual point of view and the company is in violation of the contractually agreed monthly uptime scores. Frequent restarts may also lead to a broken asset in the near future. All this represents the business context relevant to Asset Y underperforming.
Waylay Digital Twin easily makes the connection with the business context in Salesforce through the use of Salesforce Flows. In the screenshot below (Fig.3), you can see a business flow that takes the Waylay Alarm produced by our monitoring rule shown above, and use its properties to populate a Salesforce downtime record. The downtime record is then used in Salesforce to automatically calculate availability and reliability scores. Without the insights provided by Waylay Digital Twin, the scores would have been much less accurate. Furthermore, with Waylay Digital Twin, the availability and reliability scores better match the customer’s experience (an unreliable asset that restarts often).
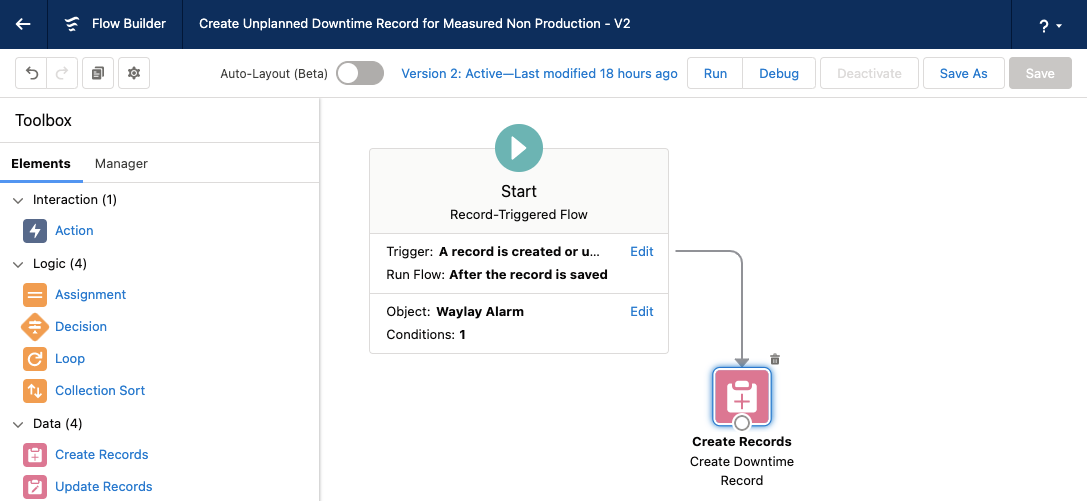
Waylay Digital Twin helps to detect downtime and effectively track down the root cause of the problem. It thus enables the asset expert to take countermeasures well in advance of any calamities. In Fig. 1, the asset timeline shows the complete history of Waylay Alarm records that have been raised by other predictive monitoring rules or diagnostic tests that were executed at the time of maintenance. In other words, it is visually straightforward to trace the symptom (frequent restart alarm) back to any previous issues (software errors after maintenance due to a broken pipe).
Conclusion
Monitoring asset uptime is key to any business that involves connected assets. Whether you use the data internally or you expose your availability and reliability KPIs through customer portals, you need a solution that can flexibly adapt to the business conditions of the asset and the customer. Waylay Digital Twin empowers business users to create such monitoring rules and compute more accurate performance KPIs quickly. Furthermore, it enables service engineers to answer the question as to why the availability and reliability are degrading.