It’s estimated that IoT applications in operations optimisation have the potential to create value of $1.2 to $3.7 trillion per year in the factory setting in 2025. Manufacturers and equipment builders are in a position to jointly create this value, thanks to new IoT technology advancements.
Equipment builders now have a clear product-oriented value offering, in the form of physical assets made to perform specific tasks for manufacturers: compressing air or pumping water, mixing liquids or cutting solids, packaging biscuits or bottling sodas. Their equipment is part of the customer’s production flow, but is bought, managed and serviced as a standalone piece. Machine builders have the unique opportunity to look beyond their standalone product offering and propose value-added services that are focusing on the overall goal of their customers: improving production output.
To unlock new service models focused on equipment monitoring and maintenance, a successful solution stack for equipment builders is made up of the right industrial hardware & connectivity (for capturing data) and integration, analytics and automation software (for taking advantage of the captured data).
Leveraging Industrial IoT sensors and gateways to capture asset and process data
Equipment and machine builders have a lot to profit from adding connectivity to their products. Internet-enabled machines are able to send information about how the machine behaves, if it’s used at its optimal set point, if it degrades ahead of time, if and when it might break, and much more.
New IIoT sensors embedded with built-in connectivity can be attached to existing industrial equipment and measure a myriad of equipment performance indicators. IIoT gateways aggregate data from multiple sensors deployed across large surface sites, via low-power wide-area (LPWA) networks such as LoRaWAN™. They do basic edge processing before sending it to the OEM’s cloud back-end. Most of the times, new IIoT gateways enable data transmission without the need to interfere in the privacy-sensitive networks of the manufacturer and enabling OTA (over the air) use cases.
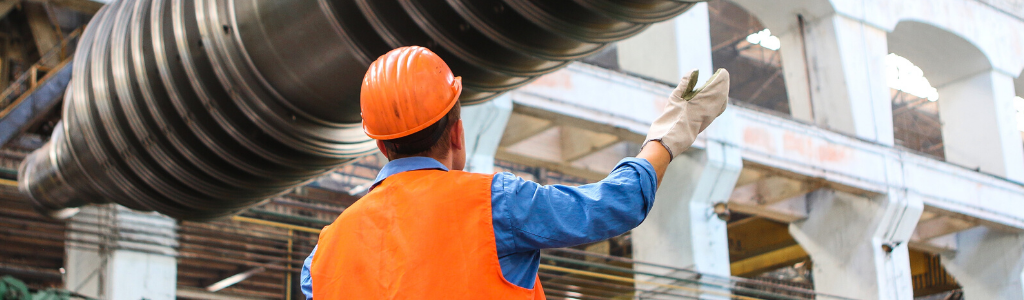
Positioning for value-added services with data integration, automation and analytics
Connected machines can bring such benefits to manufacturing customers as optimal power consumption and higher efficiency, while enabling less defects during operation and early error correction. But, as with any IoT-enabled object, they require some amount of data to be sent to the cloud, in order for most of these benefits to be realised.
Major cloud providers such as Microsoft Azure or AWS are a popular choice for equipment builders to ensure secure data collection, storage and management of the data from equipment IIoT sensors and gateways. Further on, as the velocity and volume of data can be a struggle to handle and make sense of, having the right software foundation to integrate, analyse and act is critical.
A flexible IIoT software platform such as the Waylay platform will be able to combine the expertise of the equipment builder’s domain specialists with the real data coming from the machines in order to answer questions such as:
- is the equipment used at its optimal efficiency point?
- is the equipment’s power consumption within the expected range?
- when will the equipment need maintenance?
- when will a specific part/component need to be replaced?
Integration with existing IT systems such as MESs, ERPs or NOCs (the vendor’s or the customer’s, depending on the use case) can unlock new solutions, such as automated support case handling or optimized vendor managed inventory (VMI). For example, a detected malfunction can be immediately reported in the equipment provider’s CRM system, where a support case is automaticaly created with all relevant fault information. The provider’s services team is empowered to take proactive action and reach faster problem resolution.
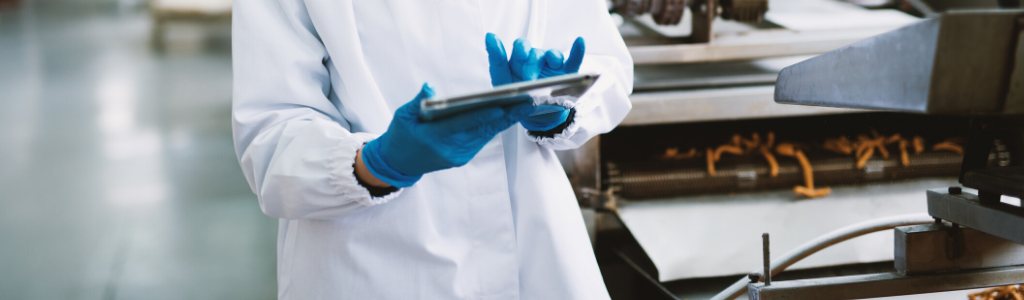
Accelerating service and solution delivery with pre-templated operator dashboards
Having a powerful data processing platform such as Waylay enables equipment builders to extract meaningful insights from near real-time equipment data, but successfully delivering this value to customers would typically require further work: building the end-user application. As end users, industrial facility and plant operators, maintenance and process engineers have specific KPIs that they want clearly shown in an IIoT application. They want simple and clear navigation and visualisation that enables immediate focus on specific pain or risk points. They reject overwhelming dashboards or too technical, developer-focused interfaces.
Building monitoring applications for users is not therefore an easy endeavour. At Waylay, we have developed the Waylay Dashboard, a turnkey solution that was built to address these specific challenges and that integrates out of the box with Waylay’s powerful Industrial IoT platform. As a solution provider, you therefore have both a full set of developer tools to enable your teams to capture and make sense of data, and a ready-to-use dashboarding application that can get you to market with user-ready apps in days instead of months or years.
Conclusion
With advancements in IIoT technology, OEMs can build more capability into their machines to ultimately support their customers to reduce production risks and costs. Building extra capabilities into machines usually means capturing and taking advantage of existing and/or new data about the condition of their machines and how they are being used.
At Waylay, we offer machine builders and OEMs an IoT platform with built-in integration with IIoT gateways for easy data capture and a full set of software tools for automation, analytics and asset and process monitoring, that accelerate IoT solution development. Moreover, we provide a flexible visualisation dashboard that can be white labeled and templated to fit your customers’ specific requirements.